

department of mechanical engineering
student development ACTIVitiES
Various number of student development activities are constantly being practiced in each classrooms, enforced by our Center of Learning and Teaching.
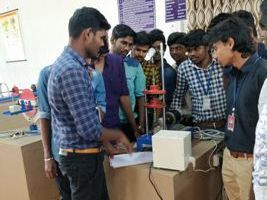
Cam and follower (Demo based learning)
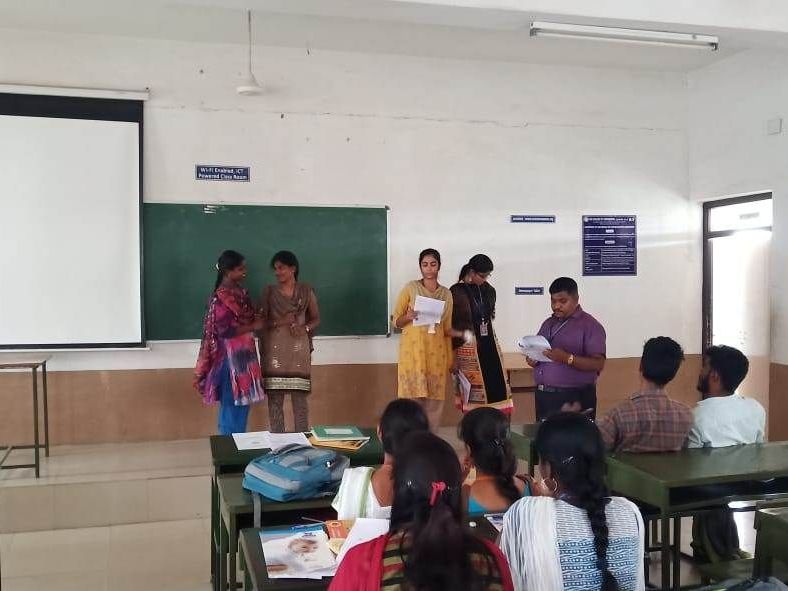
Case Based Learning HR
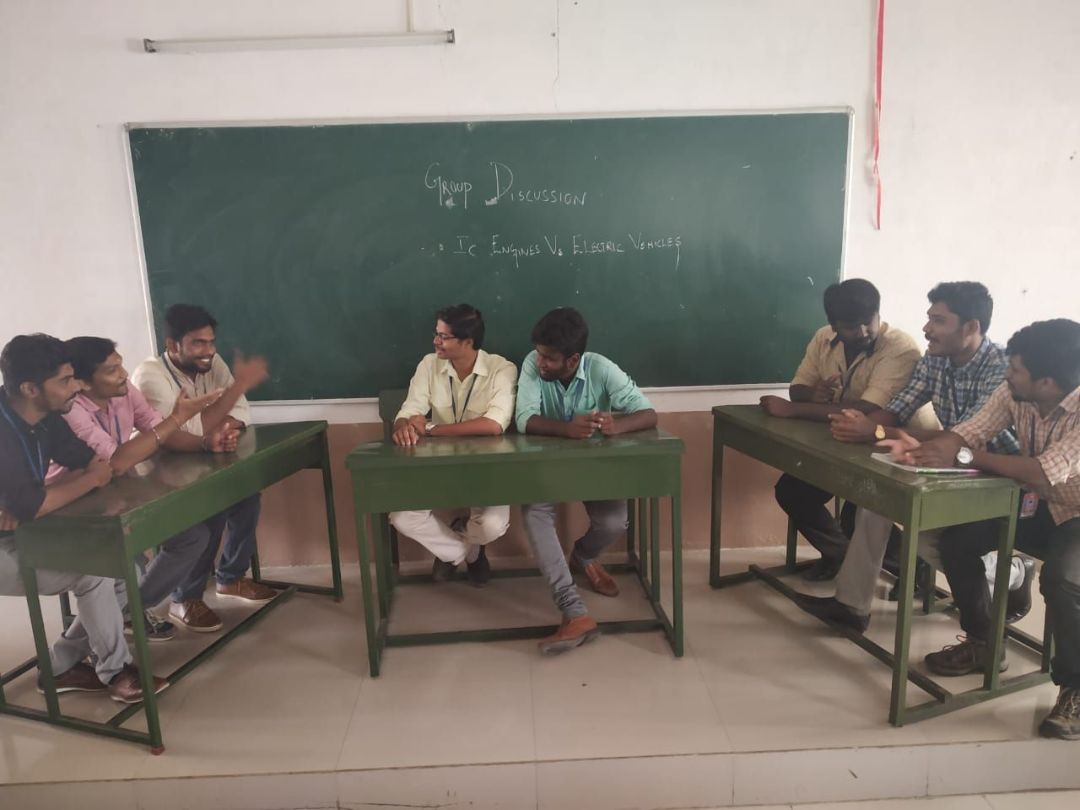
GD IC engines
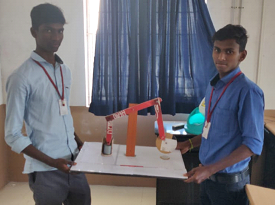
Inversion of Four bar Mechanism (Project Based Learning)
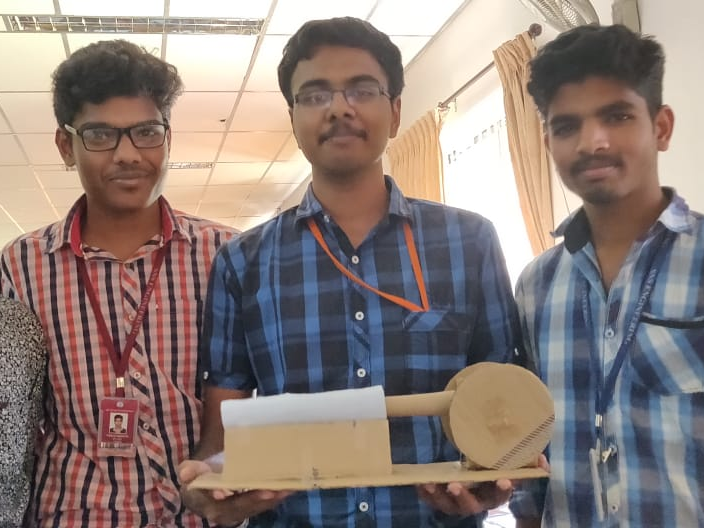
Inversion of Single Slider Crank Mechanism (Project Based Learning)
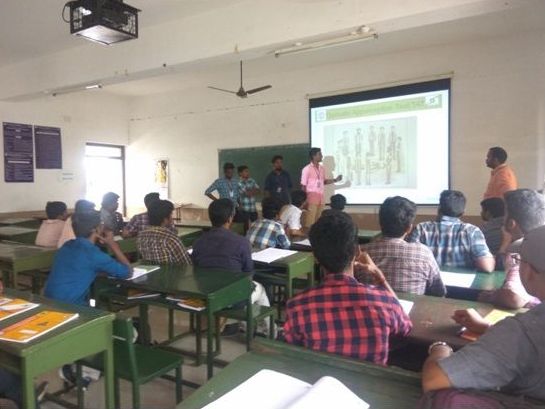
Thematic Appreciation test
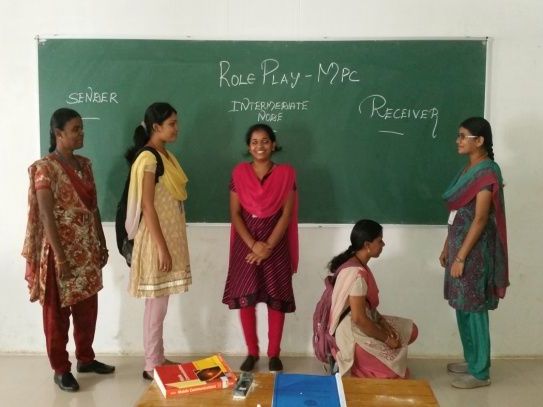
Role Play Torsion of Shafts
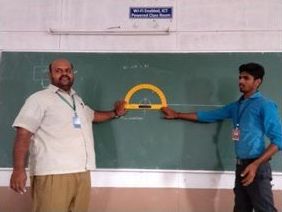
Use of Instruments
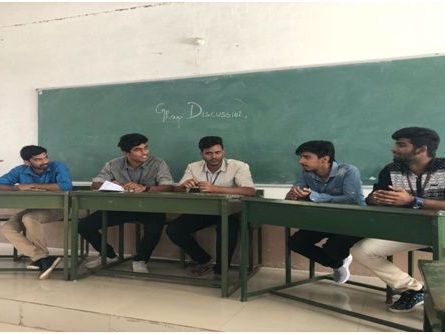
Group Discussion
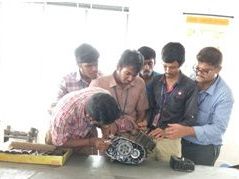
Hands on Demo
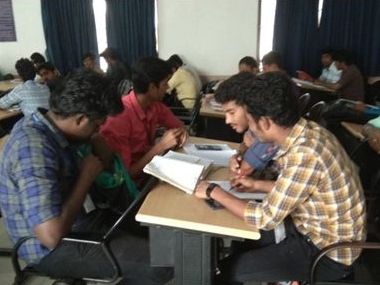
Peer Group Learning
Hands on Demo sharper: It is a customary practices to show the demo of conventional machines before the theory commencement for deep learning.
Picture Based Learning: A picture with all the details of materials is displayed. A set of students were given a randomly arranged materials name. The students will discuss and identify the same.
Think Room Kit: The think room kit is a kit to involve all the student participate in effective learning.
classroom
demo models
industrial
case study
Naturally, students are more inductive than deductive, they learn better from examples than from logic. So, we believe the use of case studies is a very effective classroom technique. Students will be provided with an industrial case study linked with the concept or subject, where the students got to explore how their learning are applied in the real world situations. This helps the students to actively engage in figuring out the principles from the examples.
Objective:
This Case study is about failing of thermocouples in ethylene cracking plant and has been taken from a Chemical manufacturing plant at south Louisiana. The problem on failing of thermocouples was identified by Thermosensors Corporation.
Problem Statement:The Thermocouples used in the effluent stream of ethylene cracking furnaces were failing frequently and drifting as much as 80° F, resulting in production slowdowns and outages. During these outages, a steam air decoke process occurred, so thermocouples and thermowells had to be inspected and failed assemblies replaced.
Solution:It is clear from the problem statement that thermocouples used now in the ethylene cracking furnaces are failing frequently and hence there is a need to replace the thermocouples and redesign the thermowells for increasing the efficiency of the plant.
There are two main types of thermocouples, base metal thermocouples and noble metal thermocouples. The base metal thermocouples are made of materials like nickel, iron and copper. Base metal thermocouples will have high sensitivity and they are less expensive. The Noble metal thermocouples are made of noble metals like platinum and rhodium. They are highly expensive, but they have ability to withstand high temperature and measure high range of temperatures.
Analysing the various types of thermocouples and taking into account the cost of the thermocouple, their withstanding capacity and measurement range it was found that both Type K and Type N thermocouples suits the requirements. Though Type N thermocouple withstands high temperature capacity of 1300 ºC and is slightly expensive, it is not best suited for this particular application. Type K thermocouples are not expensive and they can withstand the temperature of 1260ºC which is higher than the ethylene cracking furnace temperature. This Type K thermocouple will be best suited for our application and it is found that the run time of the furnace has been increased by five times after replacement. Thus the customer experienced high reliability and accuracy of temperature readings after redesign and replacement.
Objective:
This Case study is about usage of zero speed sensors in Industrial Environments and is a real time problem in most of the manufacturing industries. The Inability of the Hall Effect base zero speed sensors to sense the speed of the gears has been clearly pointed out in this case study and has been taken from Motion sensors Inc, North California.
Problem Statement:A zero speed sensor was installed to sense the rotation of a gear in a piece of heavy equipment. The location of the installation exposed the speed sensor to metal shavings and debris that were present in the environment. The existing speed sensor used a back biased Hall Effect technology which incorporated the use of a magnet. The metal debris was attracted to the magnet and accumulated around the tip of the speed sensor, over time affecting the ability of the sensor to accurately distinguish the teeth of the spinning gear.
Solution:In most of the Manufacturing Industries metal debris and shavings will be present in the environment due to the metal cutting processes. The metal particles get attracted to the hall effect sensors due to the presence of magnet inside them. During the process of continuous speed sensing, the tip of the sensor is completely covered by metal particles thereby making it incapable to sense the rotation of the gear. Thus the efficiency of the sensor is drastically reduced.
The above problem can be solved in the Industry by replacing the current sensor with RF speed sensor. In the RF speed sensor, due to the absence of magnet the metal shavings and debris are not attracted towards the tip thereby improving its speed sensing ability. It effectively removed the strong magnetic field eliminating the performance issue.
In this case study, we have discussed an average precipitation of 1170 mm rain fall and the classification of rivers in India. Further, we find the solution for water resources problems.
Mathematics is used to solve many real-world problems in industry, the physical sciences, life sciences, economics etc. This presentation is then mathematically manipulated to provide some useful information. Finally, the knowledge gained from this information should be translated into an action for the system, situation, or problem at hand.
The implementation of value stream mapping technique in pump manufacturing company. The current production rate of the line is 80 pump’s/day and this project is aimed at to improve the capability of the (Global Pumping Unit) GPU line to produce 160pump’s/day. The sub assembly and the main assembly operations capacities are depends on the manpower and there is no bottleneck to add the manpower as and when required. The aim of the work is to improve the pump productivity of the company through reducing cycle time by identify bottlenecks and non value added activities.Current state map is prepared to describe the existing position and various problem areas. Future state map is prepared to show the proposed improvement action plans. Reduction in lead time, cycle time and inventory level achieved from value stream implementation.Companies that want to improve their productivity, VSM is a good lean manufacturing tool for identifying the wastes, eliminate it and also to reduce cycle time there by productivity can be increased. They are manufacturing 80 pumps/day(2 shifts) to 160pumps / day (2 shifts ) after implementation of VSM. The current state map and Future state are drawn. Today’s future state will be tomorrow’s current state in future advanced technology will reduce the non value added activities in today’s future state map it helps to increase the productivity.Now a days, implementing the VSM seems to be a common scenario in the manufacturing industry, however getting the benefits out of it lies on the true implementation with continuous monitoring and review mechanism in place. With successful implementation of the VSM will improve the cash flow of the business supporting for its growth.
A case study of the Tabriz Tractor Manufacturing Company (TTMC) that demonstrates how GT can be applied in metal forging operations and (2) present a coding system based on the hybrid coding structure designed for the TTMC’s forging operations. In addition to these contributions, we present a Visual Basic computer software developed to classify parts in the actual forging operations of the TTMC, based on the design hybrid coding system. This classification and coding system, while developed specifically for the TTMC, should work with all forging operations. The parts classification and coding system designed for implementing the GT in the forging operation of the TTMC is described. It is difficult to adopt existing systems for industries or operations other than the forging operations of the heavy equipment industry because each industry (and the operations) has a different priority when grouping the parts. Therefore, a new classification and coding system is developed to consider, explicitly, the specific parts parameters and the production process specifications of the TTMC’s forging operation. While the system is developed specifically for the TTMC’s forging operation, it should be applicable to all forging operations in similar industries.The first digit of the above code can take the values 1, 2, 3 or 4, based on the following rules on a part’s general geometric shape.The second digit is defined following the hierarchical structure and is directly related to the first digit (general geometric shape). Subsequent digits (digits 3 to 6) follow a chain structure and are coded using more detailed geometrical specifications. The decision rules and the coding values are outlined in the Appendix. The implementation of the GT can decrease the activities and lead time relating to part design, improve company responsiveness to customer orders and streaming production processes. The implementation of a GT system that integrates part data, GT codes, operations process plans and CAD management features, as presented in this paper, can reduce repetitive activities in engineering by allowing the designs and processing plans of existing parts to be reused for parts with similar features. By reusing the existing design and plans, the forging operations can be more efficiently standardized, and the need for a production feasibility analysis is reduced. Thus, lead to a greater process reliability and production efficiency. This is very beneficial for the TTMC’s forging operations. Furthermore, such an integrated system retains and improves the organisational knowledge and memory, because part designs and processing plans can be shared more readily and such information remains with the company when experienced technical staffs leave the company.
In order to improve the perceived sound quality of diesel engines, Isuzu cooperated with Brüel & Kjær to develop mapping of Sound Quality metrics, where noise sources can be identified based on their sound character using perception-based metrics such as loudness, sharpness and roughness. Together, they also developed a new impulsiveness algorithm to clearly identify the source of impulsive noise in diesel engines. The result of the Isuzu/Brüel & Kjær project is now the world’s first commercially available sound quality metrics mapping software for beamforming and Statistically Optimal Near-field Acoustic Holography (SONAH) systems.In recent years, environmental issues have placed emphasis on vehicle emission and vehicle noise including improved engine noise performance. It is becoming increasingly important not just to reduce the radiated sound pressure, but also to improve the sound quality of vehicles for the comfort of both passengers and local residents. Isuzu regards sound quality as a key selling point and differentiatorDiesel engines make a characteristic noise known as diesel clatter, diesel nailing, or diesel knock. This is caused largely by the sudden combustion of fuel that has already evaporated when combustion starts. Although unavoidable, this sound is not desirable and it is notoriously difficult to identify precisely where the sound is coming from. Traditional microphone array techniques, such as beamforming and near-field acoustic holography (NAH) localise noise sources based on physical quantities such as sound pressure and sound intensity. However, other sources may have higher values of sound quality metrics, so the objective data in the contour plot may not accurately reflect one’s subjective perception. For example, improving the perceived sound quality of diesel engines may require the identification of noise sources emitting impulsive or rough sounds rather than having higher sound pressure level. For this reason, Isuzu got together with Brüel & Kjær to develop mapping of Sound Quality metrics, where noise sources can be identified based on their sound character using perception-based metrics such as loudness, sharpness and roughness. Together, they also developed a new impulsiveness algorithm to clearly identify the source of impulsive noise in diesel engines.As a result of the cooperation between Brüel & Kjær and Isuzu, mapping of Sound Quality metrics has been implemented in PULSE Beamforming Type 8608 and PULSE Acoustic Holography Type 8607 and is the world’s first commercially available sound quality metrics mapping software for beamforming and SONAH systems – a first class example of how Brüel & Kjær and one of its key customers worked together to develop cutting edge technology for the automotive industry.
The aim of this work is to utilize the heat energy wasted in exhaust gas of an internal combustion engine of low capacity for desalination using a submerged horizontal tube straight pass evaporator and a condensing unit, without the aid of any external energy used for pumping system. In this work a horizontal tube straight pass evaporator and water cooled condenser for condensing the evaporated steam were designed and fabricated. The experiments were conducted in a 5 hp diesel engine to analyze the performance of the submerged horizontal tube straight pass evaporator (SHTE) under various load conditions. It is evident that 3.0 l/h of saline water can be desalinated from the engine exhaust gas, without affecting the performance of the engine. More over nearly 24 l of water is heated, up to 60 °C in the condenser unit. By utilizing the heat energy in condenser water in addition to waste exhaust gas heat energy the overall efficiency of the system is enhanced and thermal pollution is also reduced considerably.
In the present case study, the methodology of designing and machining the femoral component of total knee replacement using a 3-axis Computer Numerical Control (CNC) machine is presented, and then, the results of the machining process, as well as the evaluation of implant surface quality are discussed in detail. At first, a preliminary design of the components of the knee implant is performed and the planning for the production of the femoral component is implemented in Computed Aided Manufacturing (CAM) software. Machining of complex, “sculptured” surfaces is important in various industries such as automotive, aerospace and optical components industry, as well as bioengineering. One of the main challenges concerning the machining of such surfaces is the reduction of machining time, as it is considerably difficult to achieve the required dimensional accuracy and surface quality. Apart from the use of cutting tools with special geometry, the machining strategy needs to be carefully planned in order to achieve the desired geometrical features and suitable process parameters are required to be determined as well. Thus, all of these tasks need to be appropriately addressed by the use of CAM software in order to perform the machining process of the femoral component. Then, three femoral components are machined under different process conditions and the surface quality is evaluated in terms of surface roughness. Analysis of the results indicated the appropriate process conditions for each part of the implant surface and led to the determination of optimum machining strategy for the finishing stage. The design and manufacturing of medical implants constitutes an active and highly important field of research, both from a medical and an engineering point of view. From an engineering aspect, the machining of implants is undoubtedly challenging due to the complex shape of the implants and the associated restrictive geometrical and dimensional requirements. Furthermore, it is crucial to ensure that the surface integrity of the implant is not severely affected, in order for the implant to be durable and wear resistant.
This case study focuses on the study of virtual reality in the assistance of CNC machine tool demonstration and exhibition. A commercial CNC machine tool was used in this study to illustrate the effectiveness and usability of using virtual reality for an exhibition. The adopted CNC machine tool is a large and heavy mill-turn machine with the width up to eleven meters and weighted about 35 tons. A head-mounted display (HMD) was attached to the developed VR CNC machine tool for the immersion viewing. A user can see around the 3D scene of the large mill-turn machine and the operation of the virtual CNC machine can be actuated by bare hand. Coolant was added to demonstrate more realistic operation while collision detection function was also added to remind the operator. This case study has shown that young engineers and/or students are very impressed by the VR-based demonstration while elder persons could not adapt themselves easily to the VR-based scene because of eyesight issues. However, virtual reality has successfully being adopted and integrated with the CNC machine tool in an international show. Another machine tool on laser-assisted milling machine motion simulation has also been successfully conducted to show the expandability of the VR based technology. One can conclude that VR will be adopted and paid more and more attention in the future in helping CNC machine tool promotion. Exhibition and demonstration are generally used in the promotion and sale-assistance of manufactured products. However, the transportation cost of the real goods from the vender factory to the exposition venue is generally expensive for huge and heavy commodity. With the advancement of computing, graphics, mobile apps, and mobile hardware the 3D visibility technology is getting more and more popular to be adopted in visual-assisted communication such as amusement games. Virtual reality (VR) technology is therefore used in emulating expensive small and/or huge and heavy equipment. Virtual reality can be characterized as 3D extension with Immersion, Interaction and Imagination.